Understanding the Impact of Toolpath Optimization on CNC Efficiency
Discover how toolpath optimization in CNC machining significantly improves operational efficiency, reduces costs, and enhances product quality through intelligent programming and cutting strategies.
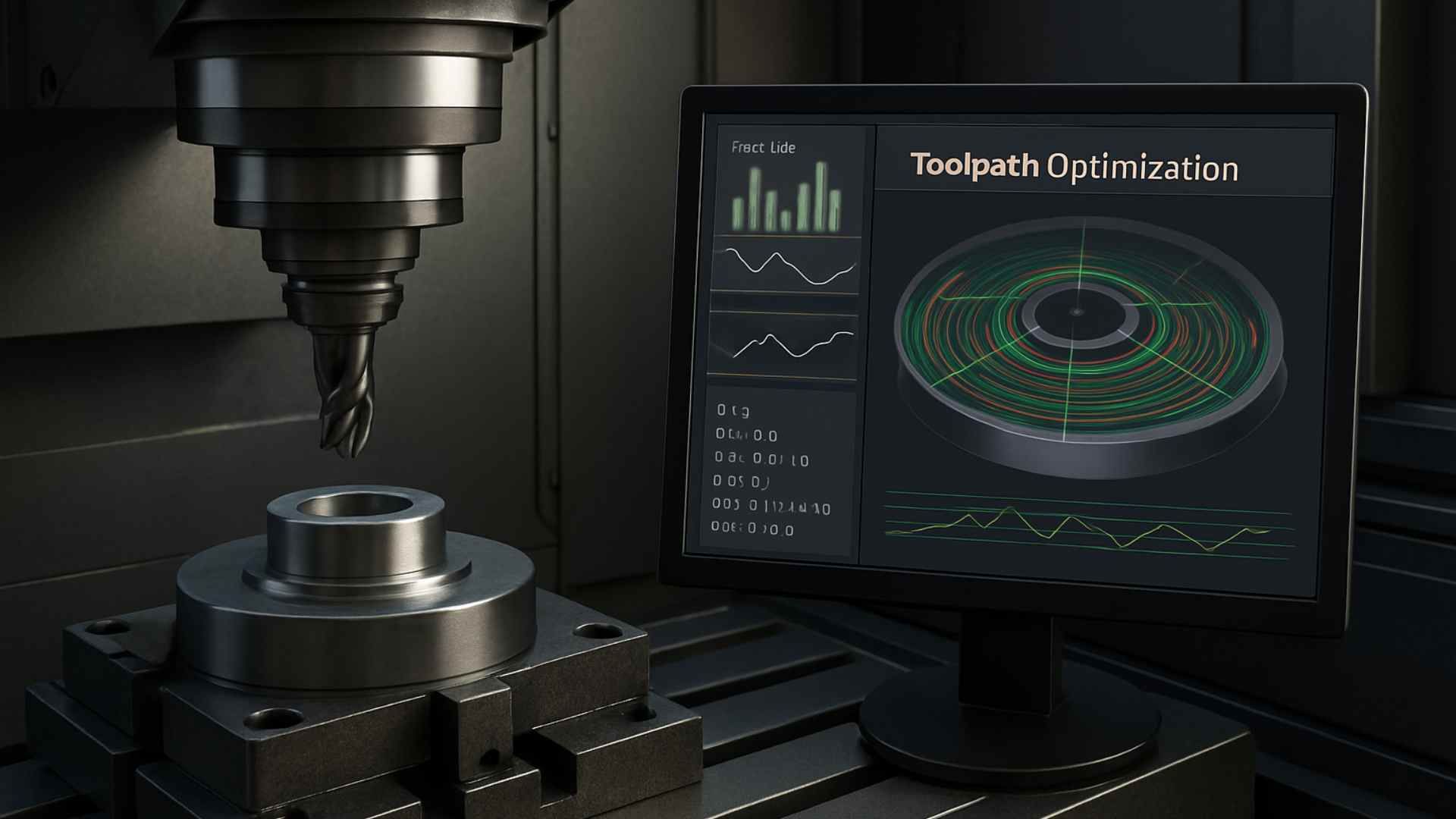
July 10, 2025
Share:
Computer Numerical Control (CNC) machining has become a cornerstone of modern manufacturing, offering precision, repeatability, and speed. However, even the most advanced CNC machines can underperform if the programming isn’t optimized. This is where toolpath optimization comes into play. By intelligently designing the path a cutting tool follows, manufacturers can unlock significant gains in efficiency, reduce machining time, lower tool wear, and improve part quality.
In this blog, we dive deep into how toolpath optimization affects CNC efficiency, the strategies involved, and how manufacturers can benefit from adopting smarter programming practices.
What is Toolpath Optimization?
In CNC machining, a toolpath refers to the route the cutting tool takes to shape the material into a desired form. Toolpath optimization is the process of refining this route to achieve the most efficient, accurate, and cost-effective cutting operation possible.
Optimization focuses on:
- Minimizing non-cutting movements
- Reducing rapid travel distance
- Avoiding redundant passes
- Maintaining consistent chip load
- Ensuring smoother transitions between cuts
An optimized toolpath leads to less machine wear, reduced cycle times, and improved output.
Why Toolpath Optimization Matters
1. Reduced Cycle Time
By eliminating unnecessary tool movements, overlapping passes, or inefficient entry/exit points, machines can complete jobs faster.
Example: A job that takes 1 hour with a standard toolpath might be completed in 45 minutes or less with an optimized one.
2. Increased Tool Life
Optimized paths manage cutting engagement and feed rates more effectively, promoting consistent chip load and reducing wear—saving on tooling costs and minimizing downtime.
3. Better Surface Finish and Tolerances
Smooth, optimized paths reduce vibration and tool deflection, leading to improved surface finish and accuracy—vital for aerospace or medical components.
4. Lower Power Consumption
Efficient toolpaths reduce spindle load and feed motor effort, lowering energy use and boosting sustainability.
5. Fewer Programming Errors
Modern CAM software reduces human error by automatically avoiding collisions, overcuts, or undercuts during path generation.
Techniques and Strategies in Toolpath Optimization
1. Adaptive Clearing
Uses a constant engagement strategy to maintain optimal chip load, allowing higher speeds and deeper cuts.
2. Trochoidal Milling
Circular toolpath motions help dissipate heat and reduce tool stress—great for hard materials.
3. Z-Level Machining
Ideal for 3D contouring; maintains consistent Z-step for better accuracy on complex surfaces.
4. Minimized Retracts and Air Cutting
Adjusts toolpaths to avoid unnecessary lifting or movement that doesn’t contribute to cutting.
5. Entry and Exit Optimization
Ramping entry instead of plunging can extend tool life and reduce part defects.
The Role of CAM Software
Toolpath optimization is often achieved using advanced CAM software like Mastercam, Fusion 360, SolidCAM, or Siemens NX. These tools offer:
- Optimization features
- Toolpath simulations
- Real-time feedback on feed rates and collisions
Modern CAM solutions often use AI algorithms to generate optimal paths based on material type, tooling, and machine constraints.
Case Study: Real-World Impact
A mid-sized aerospace component manufacturer used Fusion 360’s optimization features:
- Cycle time reduced: 28%
- Tool change frequency decreased: 40%
- Surface finish improved: 15%
- Overall production costs down: 22%
This showcases how minor programming adjustments can create major operational improvements.
Common Challenges in Toolpath Optimization
- Machine limitations: Not all machines handle high-speed or complex toolpaths
- Improper tooling: Wrong tool geometry can reduce optimization benefits
- Lack of skilled programmers: Optimization requires machining and programming expertise
- Software costs: Advanced CAM tools can be expensive for small operations
Future of Toolpath Optimization
The future lies in smart manufacturing, with real-time optimization powered by:
- AI and Machine Learning
- IoT sensor feedback
- Automated, adaptive CAM systems
Machines will self-adjust toolpaths mid-operation for even greater efficiency.
Final Thoughts
Toolpath optimization is more than a productivity hack—it’s a strategic necessity. It improves CNC efficiency, lowers costs, enhances quality, and reduces downtime. As manufacturing moves toward automation and AI-driven systems, toolpath optimization will play a central role in efficient and sustainable CNC practices.
Explore More from Sahil Machines
FAQ
The main goal is to enhance machining efficiency by reducing cycle time, minimizing tool wear, and improving surface finish.
Yes, efficient toolpaths reduce machine load and movement, which in turn lowers power consumption.
Most modern CAM software includes optimization features, but the level of functionality may vary depending on the software and version.
It maintains a constant tool engagement, allowing for faster cutting, reduced heat buildup, and longer tool life.
While optimization can benefit most CNC machines, its effectiveness depends on machine capabilities, tooling, and the complexity of the parts.
Follow Us:
Latest Posts
Get in touch with us about anything.
Connect with our team to explore the alloy solutions and machinery expertise you need.