The Science Behind Spindle Speeds: How It Affects Machining Accuracy
Spindle speed isn’t just a number—it’s the heart of machining accuracy. Learn how optimal spindle speeds enhance precision, reduce tool wear, and improve surface quality in CNC operations.
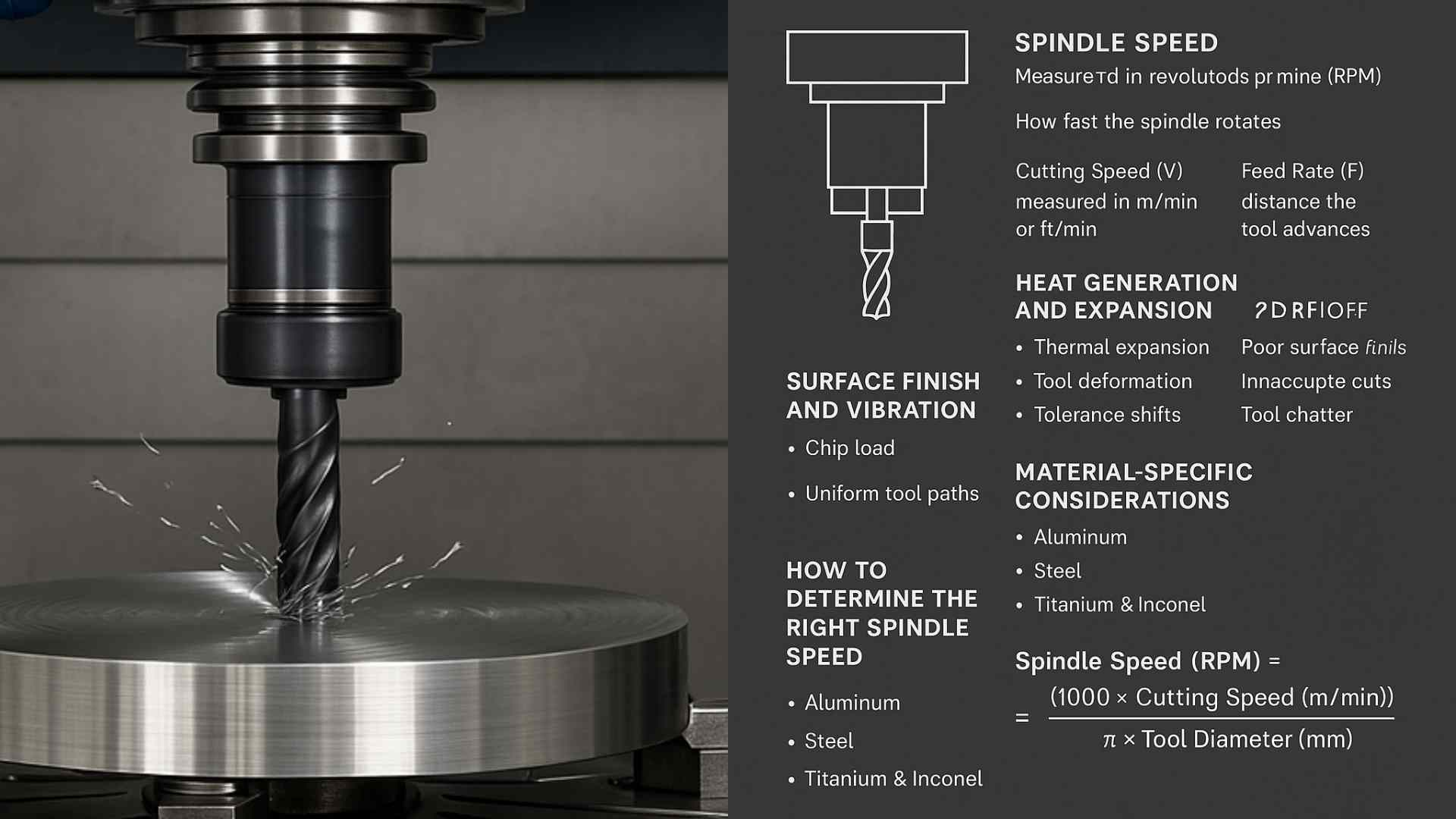
July 10, 2025
Share:
In the world of CNC machining, precision is everything. Whether you're producing aerospace components or automotive parts, even the slightest deviation can lead to rejected products or costly reworks. At the center of this precision lies a fundamental yet often overlooked factor—spindle speed.
Spindle speed directly affects everything from cutting force and vibration to surface finish and tool life. Yet, many machinists and manufacturers still struggle to find the ideal RPM for different materials, tools, and operations.
In this blog, we’ll break down the science behind spindle speeds, explore how it influences machining accuracy, and explain how to optimize it for better results.
What Is Spindle Speed?
Spindle speed, measured in Revolutions Per Minute (RPM), refers to how fast the CNC machine's spindle rotates. It determines how quickly the cutting tool moves over the material surface.
Spindle speed is closely tied to two other machining parameters:
- Cutting Speed (V): The speed at which the cutting edge moves across the material, typically measured in meters per minute (m/min) or feet per minute (ft/min).
- Feed Rate (F): The distance the tool advances per revolution or per unit of time.
Together, these factors dictate:
- How efficiently material is removed
- The temperature during cutting
- Tool wear and life expectancy
- Surface finish quality
- Dimensional accuracy
Why Spindle Speed Matters in Machining Accuracy
Let’s take a closer look at how spindle speed directly influences accuracy:
1. Heat Generation and Expansion
When spindle speed is too high, excessive friction causes heat buildup at the tool-workpiece interface. This can lead to:
- Thermal expansion of the material
- Tool deformation or softening
- Workpiece warping or tolerance shifts
Even microscopic changes in dimensions can throw off tight tolerances, especially in aerospace or medical machining.
2. Tool Wear and Breakage
High spindle speeds increase the rate of tool wear, especially if the cutting tool isn't suited for the speed or material. A worn tool leads to:
- Poor surface finish
- Inaccurate cuts
- Tool chatter or deflection
Conversely, running at very low speeds might reduce wear, but it can also result in inefficient cutting and increased cycle times.
3. Surface Finish and Vibration
Spindle speed affects the chip load—the amount of material removed per tooth per revolution. If the chip load is too high due to low spindle speeds, surface roughness increases. On the other hand, overly high speeds can cause vibrations or chatter, leaving marks on the workpiece.
A proper balance ensures:
- Smooth surfaces
- Uniform tool paths
- Consistent geometric accuracy
4. Material-Specific Considerations
Different materials require different spindle speeds for optimal results:
- Aluminum: Higher spindle speeds are often used because it's soft and easy to cut.
- Steel: Requires slower speeds to prevent overheating and tool dulling.
- Titanium and Inconel: Demand careful spindle speed control to reduce tool wear and thermal expansion.
Using the wrong speed for a material can compromise dimensional accuracy and even damage the machine.
How to Determine the Right Spindle Speed
Finding the perfect spindle speed isn’t guesswork—it’s based on science. Here's how it's typically calculated:
Spindle Speed (RPM) =
(1000 × Cutting Speed (m/min)) ÷ (π × Tool Diameter (mm))
For example, if you're machining steel at a recommended cutting speed of 50 m/min using a 10 mm tool:
RPM = (1000 × 50) ÷ (3.14 × 10) ≈ 1592 RPM
Spindle Speed (RPM) = (1000 × Cutting Speed (m/min)) ÷ (π × Tool Diameter (mm))
This formula is essential in CNC machining to calculate the optimal spindle RPM for a given cutting speed and tool diameter, ensuring precision and tool longevity.
Most CAM software and tooling manufacturers offer spindle speed recommendations based on:
- Material hardness
- Tool geometry
- Coating type
- Coolant availability
Always consult the tool manufacturer’s guidelines and test under real conditions to fine-tune your speeds.
The Role of CNC Controllers and Sensors
Modern CNC machines are equipped with smart controllers and sensors that continuously monitor:
- Actual spindle RPM
- Torque load
- Tool vibration
- Cutting forces
These systems can make real-time spindle speed adjustments to maintain accuracy and prevent tool failure. This feedback loop is essential for:
- Adaptive machining
- Automated error correction
- High-precision jobs with tight tolerances
Optimizing Spindle Speed for Machining Accuracy
Here are some best practices to optimize spindle speeds for better results:
Use the Right Tool for the Job
Tool geometry, material, and coating affect the optimal speed range. Don’t force a tool to operate outside its design limits.
Understand Material Properties
Materials have vastly different behaviors under heat and force. Match your spindle speed accordingly.
Don’t Forget Coolant
Coolant reduces friction, minimizes heat, and allows higher spindle speeds without sacrificing accuracy.
Run Test Cuts
Always perform trial runs to evaluate surface finish, vibration, and tool wear before full-scale production.
Monitor and Adjust
Use real-time monitoring tools to tweak speeds dynamically based on feedback from the machine.
The Future: AI-Powered Spindle Control
With Industry 4.0 and AI-driven CNC systems, machines are becoming more autonomous. Some cutting-edge technologies include:
- Self-adjusting spindle speeds based on AI models
- Predictive analytics to reduce tool failure
- Automated spindle speed optimization based on thousands of test cycles
These advancements will soon make manual spindle speed tuning obsolete, ensuring better accuracy, consistency, and speed.
Explore More from Sahil Machines
Looking to take your CNC processes to the next level? Check out these helpful resources:
FAQ
Excessively high spindle speeds can cause overheating, tool wear, and dimensional inaccuracy due to thermal expansion or vibration.
Spindle speed (RPM) is calculated using the formula: RPM=1000×Cutting Speedπ×Tool Diameter\text{RPM} = \frac{1000 \times \text{Cutting Speed}}{\pi \times \text{Tool Diameter}}RPM=π×Tool Diameter1000×Cutting Speed Values vary based on material and tooling.
Yes. Proper spindle speed results in smoother finishes. Too slow or too fast can lead to rough or inconsistent surfaces.
No. Each material has an optimal speed range based on its properties. Using the wrong speed can damage the tool or workpiece.
Aluminum typically allows for high spindle speeds—anywhere from 3000 to 12,000+ RPM depending on the tool and operation.
Follow Us:
Latest Posts
Get in touch with us about anything.
Connect with our team to explore the alloy solutions and machinery expertise you need.