The Role of High-Speed Machining in Modern CNC Workshops
High-speed machining (HSM) is reshaping modern CNC workshops by enhancing speed, precision, and efficiency. This blog explores the benefits, key applications, technologies, challenges, and the promising future of HSM in today’s manufacturing landscape.
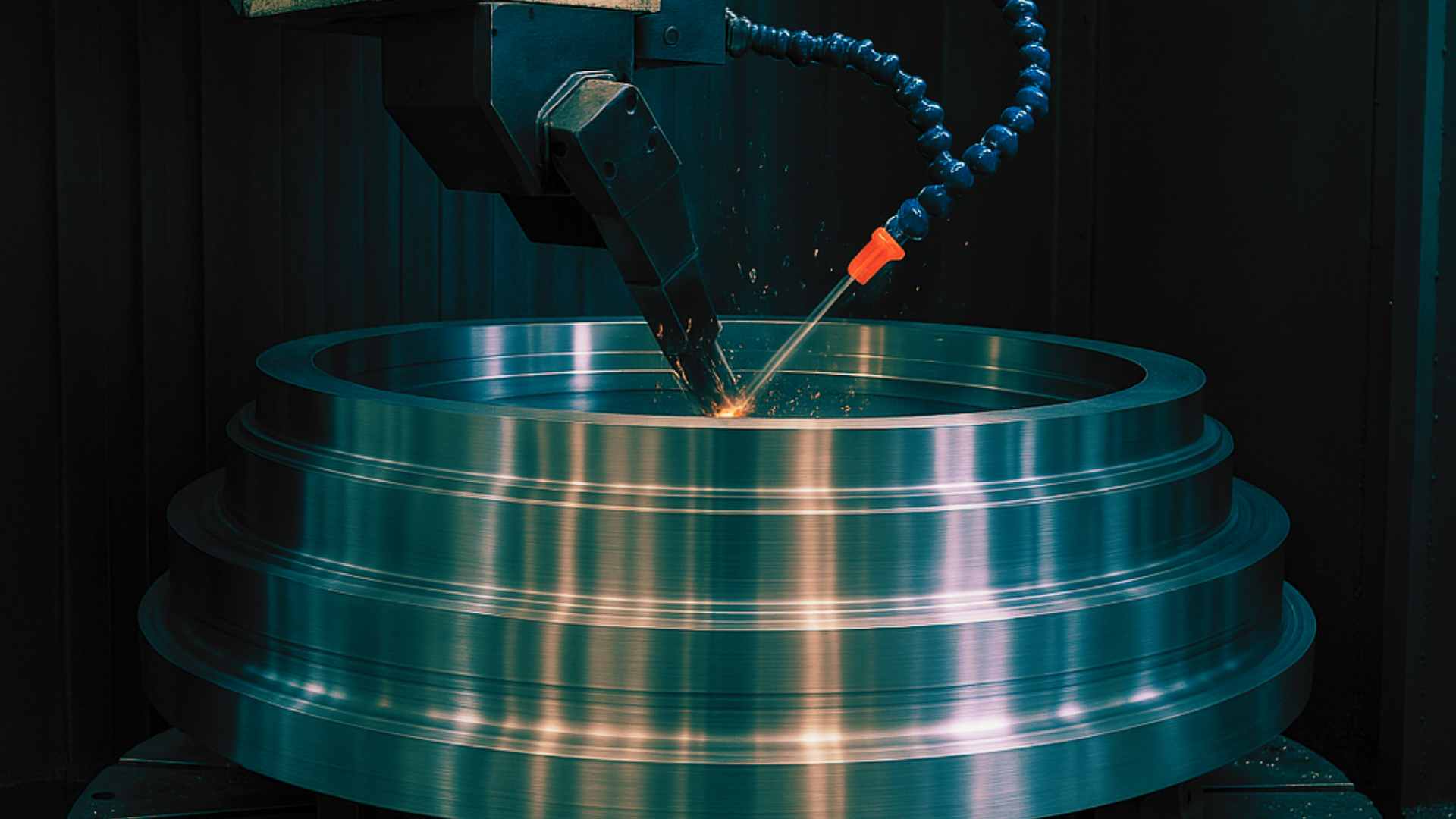
July 09, 2025
Share:
Introduction
In the world of modern manufacturing, speed and precision are critical factors that determine the success of any CNC (Computer Numerical Control) workshop. High-Speed Machining (HSM) has revolutionized CNC operations, allowing manufacturers to produce high-quality components at an accelerated pace while maintaining superior accuracy. This article explores the significance of high-speed machining in modern CNC workshops, its benefits, applications, challenges, and future potential.
What is High-Speed Machining?
High-Speed Machining (HSM) refers to a set of advanced machining techniques that utilize increased spindle speeds, faster feed rates, and specialized tooling to remove material efficiently. Unlike conventional machining, HSM minimizes heat generation and tool wear while improving surface finish and overall productivity. The technology is commonly used in aerospace, automotive, medical, and mold-making industries.
Benefits of High-Speed Machining
- Increased Productivity – Higher spindle speeds and feed rates result in faster material removal, significantly reducing machining time.
- Improved Surface Finish – HSM minimizes tool deflection and vibration, leading to smoother surface finishes and reduced post-processing requirements.
- Extended Tool Life – The efficient chip evacuation and reduced heat buildup extend the lifespan of cutting tools, reducing replacement costs.
- Enhanced Precision – Advanced control systems and reduced cutting forces lead to high accuracy in machining intricate geometries.
- Material Efficiency – HSM minimizes material waste, optimizing the use of raw materials and reducing overall production costs.
- Better Heat Management – The rapid cutting speeds help dissipate heat through chips, preventing thermal damage to the workpiece.
Applications of High-Speed Machining
- Aerospace Industry – Used for machining lightweight and heat-resistant materials like titanium and aluminum alloys to produce aircraft components.
- Automotive Sector – Helps in manufacturing precision engine components, molds, and high-performance parts.
- Medical Devices – Enables the production of intricate and high-tolerance medical implants and surgical instruments.
- Mold and Die Making – Ideal for creating detailed molds and dies with fine surface finishes and tight tolerances.
- Electronics Manufacturing – Facilitates the production of micro-components used in semiconductors and consumer electronics.
Key Technologies Behind High-Speed Machining
- High-Speed Spindles – Capable of reaching speeds above 40,000 RPM, enabling faster material removal rates.
- Advanced CNC Controls – Utilizes sophisticated algorithms to optimize cutting paths, reducing cycle times and enhancing accuracy.
- Carbide and Coated Tooling – Specialized cutting tools with coatings such as TiAlN (Titanium Aluminum Nitride) increase wear resistance and heat dissipation.
- Dynamic Motion Control – Adaptive feed rate adjustments and vibration dampening improve machining stability.
- Coolant and Lubrication Systems – High-pressure coolant systems help control heat buildup, prolonging tool life.
Challenges of High-Speed Machining
Despite its numerous advantages, high-speed machining presents several challenges that CNC workshops must address:
- Initial Investment Costs – High-speed machining requires specialized equipment, software, and tooling, leading to increased capital expenditure.
- Machine Rigidity and Stability – The high speeds necessitate machines with superior rigidity to minimize vibrations and maintain accuracy.
- Tool Wear and Selection – Choosing the right cutting tool for specific materials and applications is crucial to prevent premature wear and tool breakage.
- Programming Complexity – Optimizing tool paths for HSM requires expertise in CAM (Computer-Aided Manufacturing) software.
- Workpiece Material Considerations – Not all materials respond well to high-speed machining; proper selection and testing are essential.
Future of High-Speed Machining
The evolution of CNC machining continues to push the boundaries of speed, accuracy, and automation. Some future trends in high-speed machining include:
- Artificial Intelligence (AI) Integration – AI-powered CNC systems can optimize cutting parameters in real-time, improving efficiency.
- Hybrid Machining – Combining additive manufacturing with high-speed machining to create complex components with minimal waste.
- Enhanced Tooling Materials – The development of ultra-hard and heat-resistant cutting tools for machining exotic materials.
- IoT and Industry 4.0 – Real-time monitoring of machining operations through IoT-enabled CNC systems.
- Sustainable Machining – Adoption of eco-friendly coolants and energy-efficient machining processes to reduce environmental impact.
Conclusion
High-speed machining is transforming modern CNC workshops by enabling faster, more precise, and cost-effective manufacturing. Despite challenges such as investment costs and tool wear, its benefits far outweigh the drawbacks. With continuous advancements in CNC technology, tooling materials, and AI-driven automation, the future of high-speed machining looks promising. By adopting HSM, CNC workshops can stay competitive and meet the growing demand for high-quality, precision-engineered components.
Explore Related Machines from Sahil Machines:
FAQ
High-speed machining uses higher spindle speeds, faster feed rates, and specialized tooling to improve productivity, accuracy, and surface finish compared to conventional machining.
Common materials include aluminum alloys, titanium, stainless steel, plastics, and composite materials used in aerospace, automotive, and medical industries.
HSM reduces heat buildup and optimizes chip evacuation, minimizing tool wear and prolonging tool life compared to traditional machining methods.
Yes, but it requires investment in specialized equipment and training. Small-scale workshops can benefit from HSM by improving efficiency and reducing production costs.
Not all CNC machines are capable of high-speed machining. Machines must have high-speed spindles, rigid structures, and advanced CNC controllers to support HSM operations.
Follow Us:
Latest Posts
Get in touch with us about anything.
Connect with our team to explore the alloy solutions and machinery expertise you need.