The Benefits of Hybrid Manufacturing: Combining Additive and Subtractive Processes
Hybrid manufacturing merges additive and subtractive techniques to deliver unprecedented flexibility, precision, and efficiency. Discover how this combination is transforming the future of production.
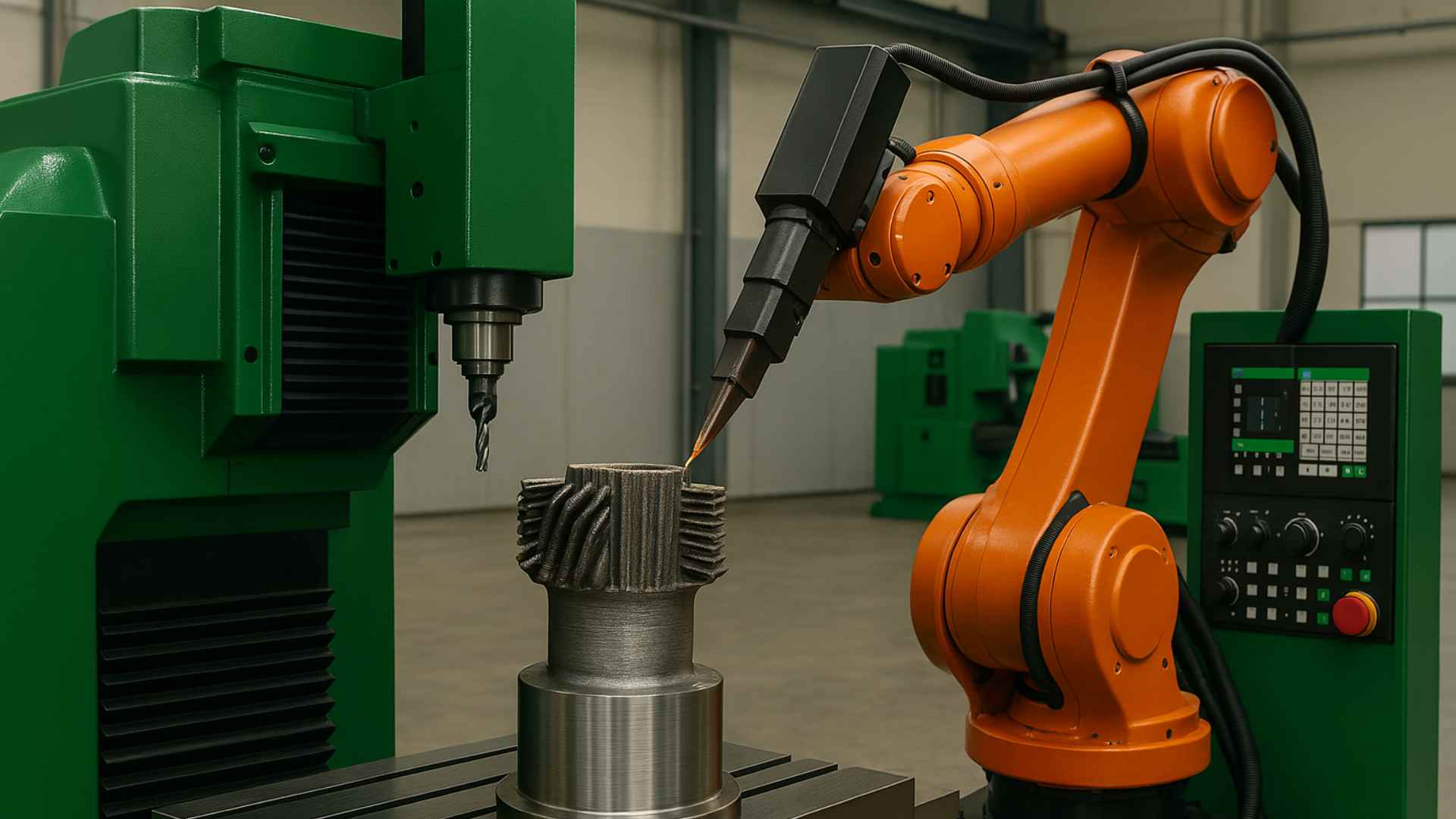
July 09, 2025
Share:
The manufacturing industry is evolving rapidly with the integration of innovative technologies that challenge traditional methods. One such breakthrough is hybrid manufacturing—a process that merges additive (such as 3D printing) and subtractive (like CNC machining) manufacturing techniques into a single, cohesive workflow.
This dual-approach opens up new possibilities in design, production speed, and part complexity, allowing manufacturers to capitalize on the strengths of both methods while minimizing their limitations. In this blog, we’ll explore the key benefits of hybrid manufacturing and why it’s gaining ground across industries from aerospace to medical devices.
What is Hybrid Manufacturing?
Hybrid manufacturing refers to the integration of additive and subtractive processes within a single machine or production sequence. Typically, additive manufacturing is used to build up material layer by layer, and subtractive manufacturing is then employed to refine the geometry, ensure tight tolerances, or create surface finishes.
The result? A single workflow that can produce complex, high-precision parts more efficiently than either method could achieve on its own.
Additive vs. Subtractive Manufacturing: A Quick Recap
Additive Manufacturing (AM):
Often known as 3D printing, this method involves building parts by adding material, typically in layers. It excels in producing complex geometries, reducing material waste, and enabling rapid prototyping.
Subtractive Manufacturing (SM):
Traditional techniques like CNC milling, turning, and grinding that work by removing material from a solid block to achieve the desired shape. It offers superior precision, surface finish, and mechanical integrity.
Why Combine Them? The Advantages of Hybrid Manufacturing
1. Unparalleled Design Flexibility
Additive manufacturing allows for the creation of complex geometries, internal channels, and lattice structures that are impossible to machine conventionally. Once the complex form is built, subtractive processes can add high-precision features, threads, or smooth surfaces.
This synergy is ideal for industries that require parts with both intricate forms and tight tolerances, such as aerospace components or medical implants.
2. Improved Accuracy and Surface Finish
Additive processes often leave behind rough surfaces or dimensional inaccuracies. Hybrid systems use CNC machining to refine the final part, ensuring precise fits, better aesthetics, and improved mechanical performance.
3. Reduced Material Waste
Additive manufacturing is already known for being material-efficient, as it builds only what’s needed. When combined with targeted subtractive finishing, hybrid manufacturing can greatly reduce overall material consumption, especially with expensive metals like titanium or Inconel.
4. Faster Prototyping and Production
Hybrid machines can print and machine a part in one setup, eliminating multiple production stages. This reduces the time spent on re-fixturing, transporting, or re-aligning parts between machines, thereby accelerating the development cycle.
5. Cost Efficiency
While standalone additive or subtractive methods have their cost considerations, hybrid systems can lead to long-term savings by:
- Reducing scrap rates
- Minimizing labor involvement
- Lowering energy consumption
- Decreasing lead times
These benefits add up, particularly in low-volume or custom manufacturing scenarios.
6. Repair and Rework Capabilities
One standout benefit of hybrid systems is their ability to repair or add material to existing parts. For instance, worn-out turbine blades can be rebuilt additively and then remachined for performance—making hybrid ideal for maintenance, repair, and overhaul (MRO) applications.
7. On-Demand Customization
With the flexibility of additive and the accuracy of subtractive processes, manufacturers can quickly adapt designs and produce customized components in small batches—perfect for medical prosthetics, personalized tools, or one-off parts.
Industries Benefiting from Hybrid Manufacturing
- Aerospace: Lightweight yet strong parts, internal cooling channels, and intricate components.
- Medical: Custom implants, prosthetics, and surgical tools with perfect fit and finish.
- Automotive: Prototyping and tooling with improved turnaround and material savings.
- Energy: Complex turbine components with extended life via repair and rebuild.
- Tooling: Precision molds and dies with optimized geometries for heat dissipation.
Challenges and Considerations
While hybrid manufacturing offers many benefits, it also comes with challenges:
- High initial investment: Hybrid machines are more expensive than traditional setups.
- Software complexity: Coordinating additive and subtractive operations requires advanced CAM tools and integration.
- Skilled workforce: Operators must understand both 3D printing and CNC machining principles.
- Material limitations: Not all materials are compatible with hybrid systems yet, especially polymers or composites.
Despite these challenges, ongoing innovations in hardware, software, and training are making hybrid manufacturing more accessible and scalable.
The Future of Hybrid Manufacturing
As Industry 4.0 technologies evolve, hybrid manufacturing will continue to play a crucial role in smart factories. The integration of AI, sensors, and IoT will enable machines to monitor material behavior, optimize paths in real time, and adapt processes for optimal results.
Additionally, advances in multi-material printing and in-situ quality control will further boost hybrid’s capabilities, making it a cornerstone of digital manufacturing ecosystems.
Final Thoughts
Hybrid manufacturing is more than just a technological fusion—it’s a strategic shift that offers the best of both worlds. By combining the creativity of additive manufacturing with the precision of subtractive techniques, manufacturers can push the boundaries of what’s possible in design, production, and innovation.
Whether you're building the next generation of jet engines or crafting custom dental implants, hybrid manufacturing opens up a realm of speed, efficiency, and functionality that standalone methods can’t match.
As the manufacturing landscape grows more competitive and customer demands more complex, the future belongs to those who embrace this hybrid approach to making things smarter, faster, and better.
Explore More from Sahil Machines
FAQ
Hybrid manufacturing combines additive and subtractive processes—typically 3D printing and CNC machining—within one workflow or machine to leverage the strengths of both.
Additive manufacturing builds complex shapes, while subtractive processes refine the part for improved accuracy, surface finish, and dimensional tolerances.
Yes, especially for complex parts, repairs, or small batch production, as it reduces waste, lowers tooling costs, and shortens production time.
Aerospace, medical, automotive, energy, and tooling industries commonly use hybrid manufacturing for its precision, flexibility, and ability to produce intricate components.
High equipment cost, material limitations, complex software requirements, and the need for skilled operators are current limitations.
Follow Us:
Latest Posts
Get in touch with us about anything.
Connect with our team to explore the alloy solutions and machinery expertise you need.