Meeting Heavy-Duty Demands with Precision Turning Lathes
Precision turning lathes deliver high accuracy and power for machining tough materials in industries like aerospace, automotive, and oil & gas. Discover their key features, applications, and how they’re shaping the future of manufacturing.
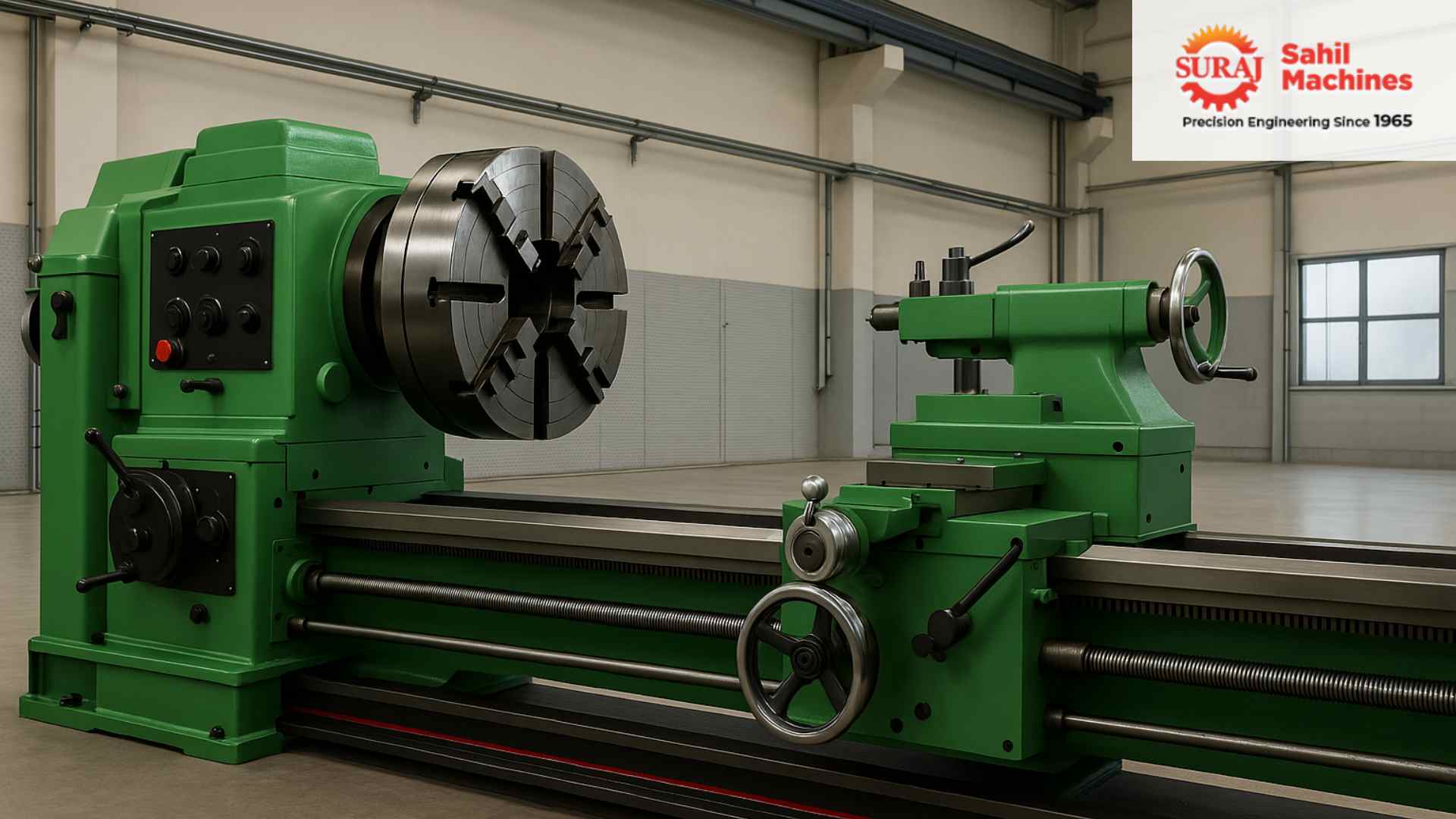
July 09, 2025
Share:
Introduction
In industries where precision, durability, and efficiency are paramount, precision turning lathes play a crucial role in meeting heavy-duty machining demands. These machines provide the accuracy and power needed to shape large and tough materials, making them indispensable in sectors such as aerospace, automotive, and heavy engineering.
This blog explores the significance of precision turning lathes, their applications, advantages, and why they continue to be the backbone of modern manufacturing.
Understanding Precision Turning Lathes
A precision turning lathe is a specialized machine tool designed for high-accuracy machining of cylindrical components. Unlike conventional lathes, these machines offer enhanced stability, precision, and control, making them suitable for machining heavy-duty materials with tight tolerances.
Key Features of Precision Turning Lathes:
- High-torque spindle motors: Ensures smooth and powerful cutting, even on hard materials.
- Heavy-duty bed and construction: Provides stability and reduces vibrations during machining.
- Precision control systems: Allows for ultra-fine adjustments to maintain accuracy.
- Automated functions (CNC integration): Enhances efficiency for mass production.
- Versatility in tooling: Supports a wide range of cutting tools and attachments for complex machining tasks.
Applications of Precision Turning Lathes
Precision turning lathes are widely used in various industries that require meticulous craftsmanship and high-performance machining.
1. Aerospace Industry
Used to manufacture critical aircraft components such as turbine shafts, landing gear parts, and engine casings with ultra-high precision.
2. Automotive Industry
Ideal for producing engine components, transmission parts, and axles that demand consistency and high-performance standards.
3. Oil and Gas Sector
Handles heavy-duty machining of drill collars, casing tubes, and valve components for high-pressure environments.
4. Heavy Equipment Manufacturing
Used for crafting industrial rollers, hydraulic cylinders, and more for construction, mining, and material handling.
5. Medical Equipment Production
Manufactures surgical tools, orthopedic implants, and diagnostic components with tight tolerances and superior finishes.
6. Defense and Military Applications
Supports production of weapon parts, vehicle armor components, and aerospace defense systems with mission-critical accuracy.
Advantages of Precision Turning Lathes
1. Unmatched Accuracy and Consistency
Delivers dimensional accuracy to micrometer levels—ideal for precision-critical sectors.
2. Heavy-Duty Machining Capability
Machines hard materials like titanium, stainless steel, and alloys with ease.
3. Increased Production Efficiency
CNC integration reduces human error, enhances consistency, and boosts output.
4. Superior Surface Finish
Reduces or eliminates the need for secondary finishing due to smooth output quality.
5. Longevity and Durability
Built to last with minimal breakdowns and long lifecycle, ensuring a strong ROI.
6. Versatility Across Materials
Capable of machining everything from hardened steel to composites.
Challenges and Considerations
- High Initial Investment: CNC precision lathes require significant upfront capital.
- Skilled Operator Requirement: Needs trained professionals for effective operation.
- Maintenance Needs: Periodic calibration and servicing required for optimal accuracy.
- Not Ideal for Low-Volume Runs: Traditional lathes may be more cost-effective in small-batch production.
Despite these, the value they offer far outweighs the drawbacks.
Future Trends in Precision Turning Lathes
Industry 4.0 and Smart Machining:
- AI Integration: Self-diagnostics and predictive maintenance.
- Advanced Automation: Real-time monitoring and adaptive CNC programming.
- Hybrid Manufacturing: Combining turning, milling, and additive manufacturing.
- Sustainable Practices: Eco-friendly cooling and lubrication systems.
- Custom Adaptive Tooling: Enhancing flexibility in batch production.
These innovations will keep precision lathes relevant and indispensable.
Conclusion
Precision turning lathes are foundational to industries that demand excellence in machining. Whether it’s aircraft components or surgical tools, these machines deliver consistent, high-precision results.
As manufacturing evolves, so too will these machines—embracing AI, automation, and sustainability. For both mass production and specialized work, precision lathes are and will remain a key asset.
🔗 Related Links from Sahil Machines
Tags
#PrecisionLathe
#HeavyMachining
#SahilCNC
#TurningMachine
#Industry40
#CNC
#AutomotiveMachining
#OilGasMachinery
FAQ
Precision turning lathes offer higher accuracy, better rigidity, and advanced control systems compared to conventional lathes, making them suitable for high-tolerance machining.
Yes, heavy-duty precision turning lathes are specifically designed to accommodate large-diameter and long workpieces, making them ideal for industries like aerospace and oil & gas.
CNC precision lathes automate cutting processes, reducing human error, increasing production speed, and ensuring consistent part quality.
These lathes can work with a variety of materials, including steel, aluminum, titanium, brass, and composite materials.
While the initial investment is high, the long-term benefits of accuracy, efficiency, and durability make them a valuable asset, even for smaller operations.
Follow Us:
Latest Posts
Get in touch with us about anything.
Connect with our team to explore the alloy solutions and machinery expertise you need.