The Impact of New Tooling Technologies on CNC Performance
Discover how the latest tooling technologies are enhancing CNC machine performance with improved accuracy, speed, and efficiency. Explore key innovations, industry applications, and future trends in smart manufacturing.
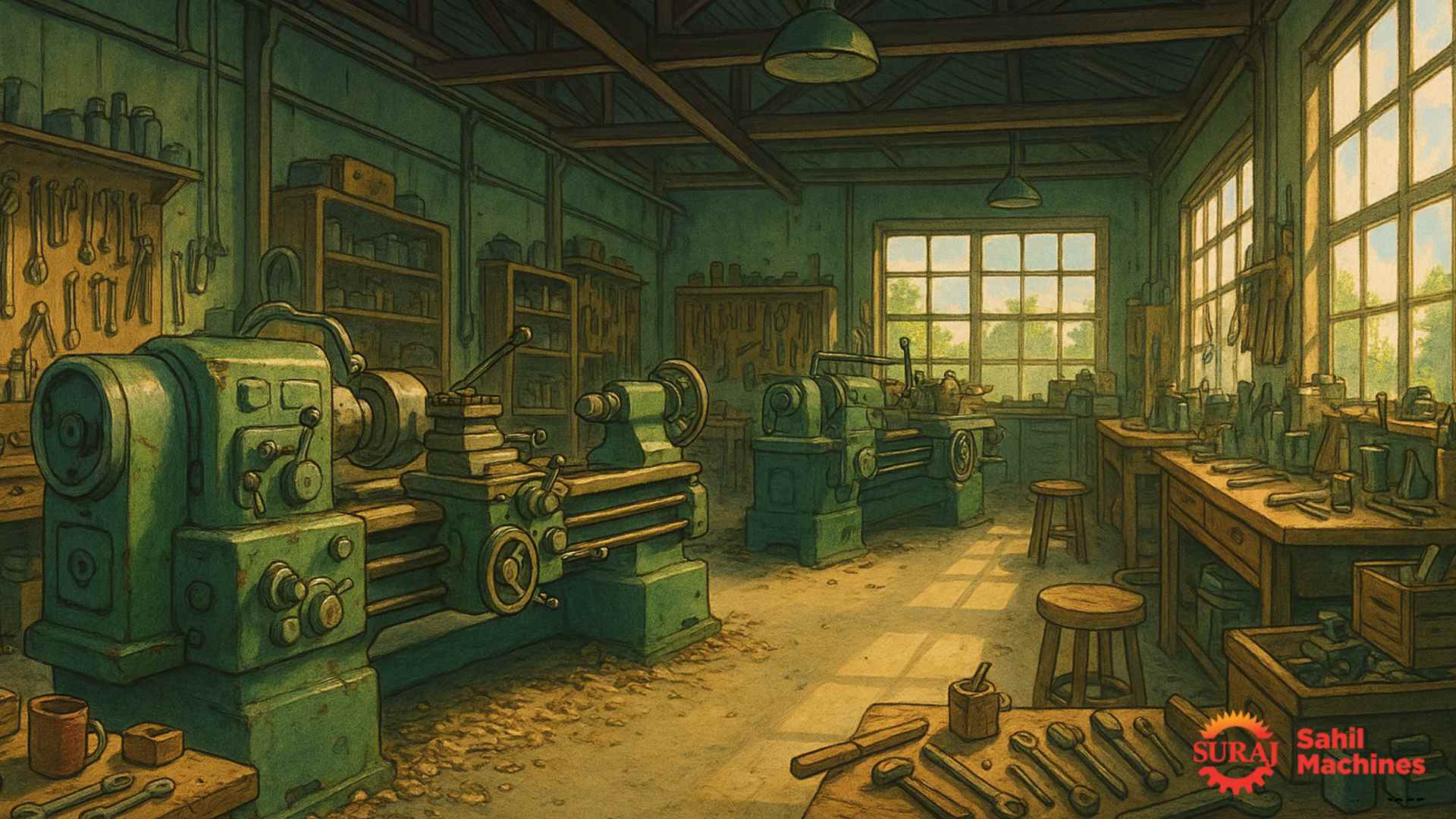
July 09, 2025
Share:
Introduction
Computer Numerical Control (CNC) machines have transformed the manufacturing industry by automating and enhancing the precision of machining processes. The continuous evolution of tooling technologies has played a critical role in improving CNC performance. From advanced cutting tools to adaptive machining systems, new innovations are driving greater accuracy, efficiency, and cost-effectiveness.
In this blog, we’ll explore how new tooling technologies are impacting CNC performance, the benefits they bring, and the future trends shaping the industry.
1. The Evolution of CNC Tooling Technologies
CNC machining relies heavily on the tools used to cut, shape, and finish materials. Traditional tooling methods were effective but often lacked the precision, durability, and adaptability that modern manufacturing demands.
With advancements in materials, coatings, and smart technologies, CNC tooling has become significantly more efficient.
🔧 Key Innovations in CNC Tooling:
-
Carbide and Ceramic Tools
Offer higher resistance to wear and heat, improving tool life and cutting performance. -
Coated Tools (PVD and CVD)
Reduce friction and increase lifespan with Physical and Chemical Vapor Deposition coatings. -
Diamond-Coated and CBN Tools
Ideal for cutting extremely hard materials, maintaining accuracy over long runs. -
Smart Tooling Technologies
Embedded with sensors for real-time data on temperature, wear, and performance—enabling predictive maintenance.
2. How New Tooling Technologies Improve CNC Performance
The integration of advanced tooling technologies into CNC machining offers numerous advantages:
✅ Enhanced Precision and Accuracy
New tooling materials and coatings reduce deflection and wear, resulting in more accurate machining.
Example: Micro-grain carbide tools retain sharpness longer—ideal for aerospace and automotive parts.
⚡ Increased Productivity and Speed
High-performance tools allow for faster spindle speeds and feed rates, reducing cycle time.
Example: High-speed steel (HSS) with cobalt resists heat and allows for faster cutting.
🔁 Reduced Tool Wear and Extended Lifespan
Durable coatings and advanced materials reduce wear, leading to fewer replacements and reduced downtime.
Example: TiAlN-coated tools resist oxidation and heat for high-temp applications.
📡 Adaptive and Predictive Machining
Smart tools with IoT and AI monitor wear, load, and performance, enabling real-time alerts and auto-optimizations.
Example: Tool condition monitoring systems detect wear and send alerts to prevent tool failure.
3. The Impact on CNC Applications Across Industries
Advanced tooling has revolutionized CNC machining across sectors:
✈ Aerospace Industry
- Precision machining of turbine blades and engine casings
- Impact: Improved finishes, reduced material waste, tighter tolerances
🚗 Automotive Industry
- Production of engine parts, axles, and suspension components
- Impact: Faster cycle times, better surface finishes, lower cost per part
🏥 Healthcare Industry
- Intricate surgical instruments and implants
- Impact: Biocompatible materials, ultra-precise shapes, consistent outputs
📱 Electronics Industry
- Miniaturized parts for consumer and industrial electronics
- Impact: High-precision micro-tooling, minimal material waste
4. Emerging Trends in CNC Tooling Technologies
As CNC machining continues to evolve, several trends are shaping the next phase of innovation:
- AI & Machine Learning: Optimized tool paths, self-calibration, and real-time performance analytics
- Hybrid Manufacturing: Integration of additive and subtractive processes
- Cryogenic Machining: Using liquid nitrogen to control heat and extend tool life
- Advanced Coatings & Materials: Nanocomposites and reinforced carbides for extreme durability
5. Benefits of Adopting New Tooling Technologies
Manufacturers that embrace advanced CNC tooling experience the following:
- Higher Production Efficiency: Faster and more accurate machining
- Reduced Operating Costs: Long-lasting tools reduce replacement costs
- Improved Product Quality: More consistent and precise outputs
- Greater Flexibility: Handle diverse materials and complex geometries
- Enhanced Sustainability: Reduced material waste and energy usage
Conclusion
New tooling technologies are revolutionizing CNC performance—boosting precision, productivity, and durability. From diamond-coated tools to AI-integrated systems, modern tooling is reshaping what's possible in manufacturing.
As these innovations continue to evolve, CNC machines will become even more flexible, intelligent, and sustainable, securing their position as vital tools across industries.
🔗 Internal Links
- CNC Flat Bed Lathes
- Heavy-Duty Turning Lathes
- CNC Vertical Machining Centers (VMC)
- Sales and Service Support
- Contact Sahil Machines
📚 Read More from Our Blog
- All You Need to Know About Heavy-Duty Turning Lathes
- All About Vertical Turning Lathe Machines
- What is CNC Machining?
🏷 Tags
#CNCMachining
#ToolingTechnology
#SahilCNC
#PrecisionMachining
#Industry40
#ManufacturingInnovation
#AdvancedTooling
#SmartMachining
FAQ
CNC tooling technology refers to the cutting tools, attachments, and systems used in CNC machines to shape and modify materials with precision and efficiency. It includes advanced coatings, materials, and sensor-based tools that enhance machining performance.
Smart tooling systems use sensors and IoT capabilities to monitor tool wear, temperature, and performance. They provide real-time data, enabling predictive maintenance, reducing downtime, and enhancing machining accuracy.
Carbide, ceramic, and cubic boron nitride (CBN) are among the most durable CNC tooling materials. They offer high resistance to wear, heat, and deformation, making them ideal for long production runs.
Cryogenic machining uses liquid nitrogen or carbon dioxide to cool the tool and workpiece, reducing heat and tool wear. This results in longer tool life, improved surface finishes, and better machining performance.
The future of CNC tooling will see increased adoption of AI-powered optimization, hybrid machining (CNC + 3D printing), and enhanced coatings for extreme durability. These innovations will continue to enhance precision, efficiency, and cost-effectiveness.
Follow Us:
Latest Posts
Get in touch with us about anything.
Connect with our team to explore the alloy solutions and machinery expertise you need.