Exploring the Use of Superalloys in CNC Machining for Extreme Environments
Discover how superalloys are transforming CNC machining in extreme environments by offering unmatched strength, corrosion resistance, and thermal stability in aerospace, energy, and medical sectors.
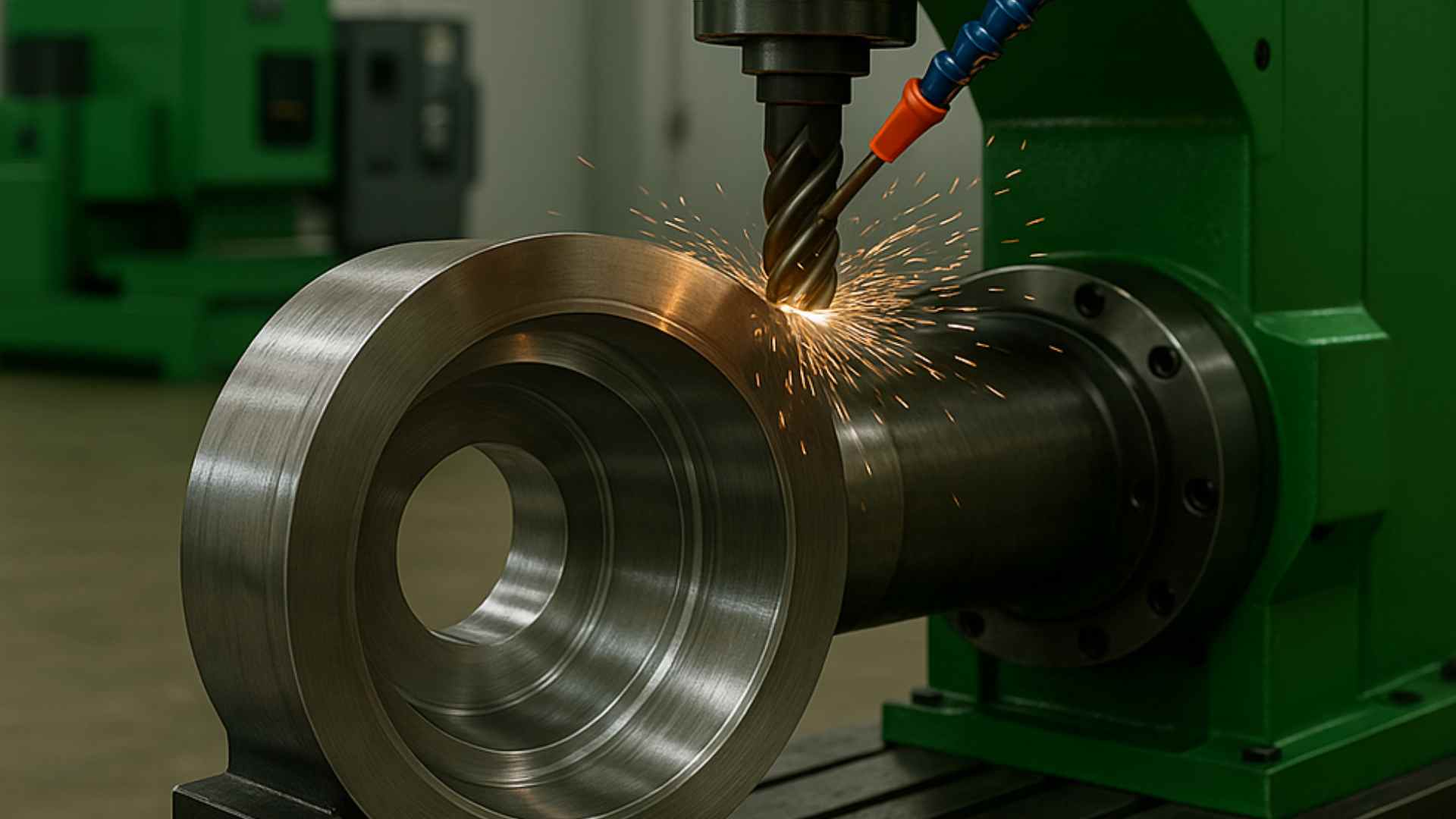
July 09, 2025
Share:
In the relentless pursuit of technological advancement, industries that operate in extreme conditions—such as aerospace, power generation, marine, and medical sectors—demand materials that don’t just withstand stress but thrive under it.
Enter superalloys, the backbone of high-performance applications where regular metals simply won’t survive. Their superior strength, resistance to heat and corrosion, and long-term durability make them the go-to choice for extreme environments. However, these same properties that make superalloys ideal for harsh conditions also make them one of the most challenging materials to machine.
This blog dives deep into what superalloys are, why they’re indispensable in demanding industries, and how CNC machining techniques are evolving to handle them with increasing precision and efficiency.
What Are Superalloys?
Superalloys, also known as high-performance alloys, are a group of metal alloys specifically engineered to maintain their strength, shape, and functionality under extreme stressors—especially high heat and corrosive environments.
They are typically based on:
- Nickel-based superalloys – e.g., Inconel, Hastelloy, Waspaloy
- Cobalt-based superalloys – often used in medical or wear-resistant parts
- Iron-nickel-based superalloys – like Incoloy, offering a cost-effective alternative
These alloys can operate in temperatures exceeding 1000°C, making them essential for components like turbine blades, heat exchangers, and combustion chambers.
Applications of Superalloys in Extreme Environments
Thanks to their unique composition and metallurgical characteristics, superalloys are used in a wide range of industries. Here are some of the most common applications:
Aerospace
Superalloys are crucial in manufacturing jet engines, turbine blades, exhaust systems, and airframe components. These parts must endure tremendous heat, stress, and corrosive gases at high altitudes.
Power Generation
Gas turbines and heat exchangers in nuclear reactors rely heavily on superalloys for their ability to maintain strength and stability at extreme temperatures and pressures.
Medical Sector
Cobalt-based superalloys are often used in orthopedic implants and surgical instruments due to their excellent biocompatibility, resistance to wear, and strength.
Marine and Oil & Gas
Components exposed to saltwater, brine, and deep-sea pressure—such as pumps, valves, and drilling equipment—leverage the corrosion resistance and toughness of superalloys.
In each of these scenarios, failure is not an option. These industries rely on the unmatched reliability that superalloys provide.
Why Machining Superalloys Is Challenging
Despite their incredible properties, superalloys pose significant challenges when it comes to CNC machining. Here’s why:
- Work Hardening: Superalloys tend to harden quickly as they are cut, making it harder for tools to continue machining efficiently.
- Low Thermal Conductivity: These materials don’t dissipate heat well, resulting in excessive temperatures in the cutting zone.
- Abrasiveness: Superalloys often contain carbide particles that wear down tools quickly.
- Built-Up Edge (BUE): Material adhesion to the cutting edge can lead to poor surface finish and higher tool pressure.
These factors demand specialized machining strategies, high-performance tools, and precise process control.
CNC Machining Techniques for Superalloys
Machining superalloys is possible—but it requires a well-thought-out strategy that blends the right tools, parameters, and cooling systems. Let’s explore how CNC machining meets these demands:
1. Tool Selection
- Carbide tools are standard, but CBN (Cubic Boron Nitride) and ceramic inserts are also widely used.
- Coatings like TiAlN (Titanium Aluminum Nitride) or AlTiN help reduce heat and wear.
- Tools with sharper cutting edges lower cutting forces and reduce friction.
2. Cutting Parameters
- Lower cutting speeds help reduce heat generation.
- Higher feed rates prevent localized work hardening.
- Shallow depth of cut minimizes tool stress and vibration.
3. Coolant and Lubrication Strategies
- High-pressure coolant systems clear chips and cool the work area.
- Cryogenic cooling, using liquid nitrogen, is being adopted in aerospace applications.
4. Advanced CAM Programming
- Adaptive toolpaths maintain a constant chip load.
- Dynamic feed rate control optimizes cutting performance.
- Simulation capabilities help detect collisions before real-world machining.
5. Real-Time Monitoring
- Vibration sensors detect chatter and tool wear.
- Tool wear monitoring systems help prevent tool breakage.
- Force sensors ensure cutting conditions stay within safe parameters.
Benefits of CNC Machining for Superalloys
Despite the complexities involved, CNC machining remains the most reliable way to manufacture intricate, high-performance components from superalloys. The advantages include:
- Precision & Repeatability: Essential for aerospace and medical components.
- Complex Geometry: 5-axis CNC machines allow for multi-angle machining.
- Superior Surface Finish: High-quality finishes with minimal post-processing.
- Faster Prototyping: CNC enables rapid development and testing of complex parts.
Future Outlook: Smart Machining of Superalloys
As industries push boundaries, so does the need for smarter machining technologies. The future of superalloy machining is increasingly digital and automated:
- AI-Driven Toolpaths: Algorithms suggest real-time adjustments for optimal performance.
- Digital Twins: Simulate machining virtually to fine-tune settings.
- Hybrid Manufacturing: Combine additive and subtractive methods to reduce waste.
Explore More from Sahil Machines
Want to know how high-end CNC machines tackle superalloys with ease? Dive deeper:
- CNC Turning Centers for High-Performance Alloys
- Vertical Machining Centers for Precision Machining
- Advanced Cooling Systems in CNC Machines
Ready to elevate your machining game with reliable CNC solutions? Sahil Machines is here to help.
FAQ
Inconel 625 & 718, Hastelloy, Waspaloy, Monel, and Rene alloys are among the most used due to their exceptional heat and corrosion resistance.
Their high strength, work hardening, and low thermal conductivity make them tough on tools and difficult to cut without overheating.
With the right setup—optimized parameters, tool coatings, and cooling systems—modern CNC machines can effectively machine superalloys.
Aerospace engines, nuclear power plants, medical implants, marine systems, and oil & gas pipelines are the primary applications.
Use of coated tools, reduced cutting speeds, high-pressure cooling, and advanced CAM software significantly improve tool life.
Follow Us:
Latest Posts
Get in touch with us about anything.
Connect with our team to explore the alloy solutions and machinery expertise you need.