Exploring Multi-Material Machining: Challenges and Innovations in CNC Technology
Multi-material machining is transforming CNC technology by enabling the processing of different materials in a single cycle. This blog explores the unique challenges—like tool wear and thermal expansion—and how innovations like hybrid machines and AI-driven toolpath optimization are reshaping modern manufacturing.
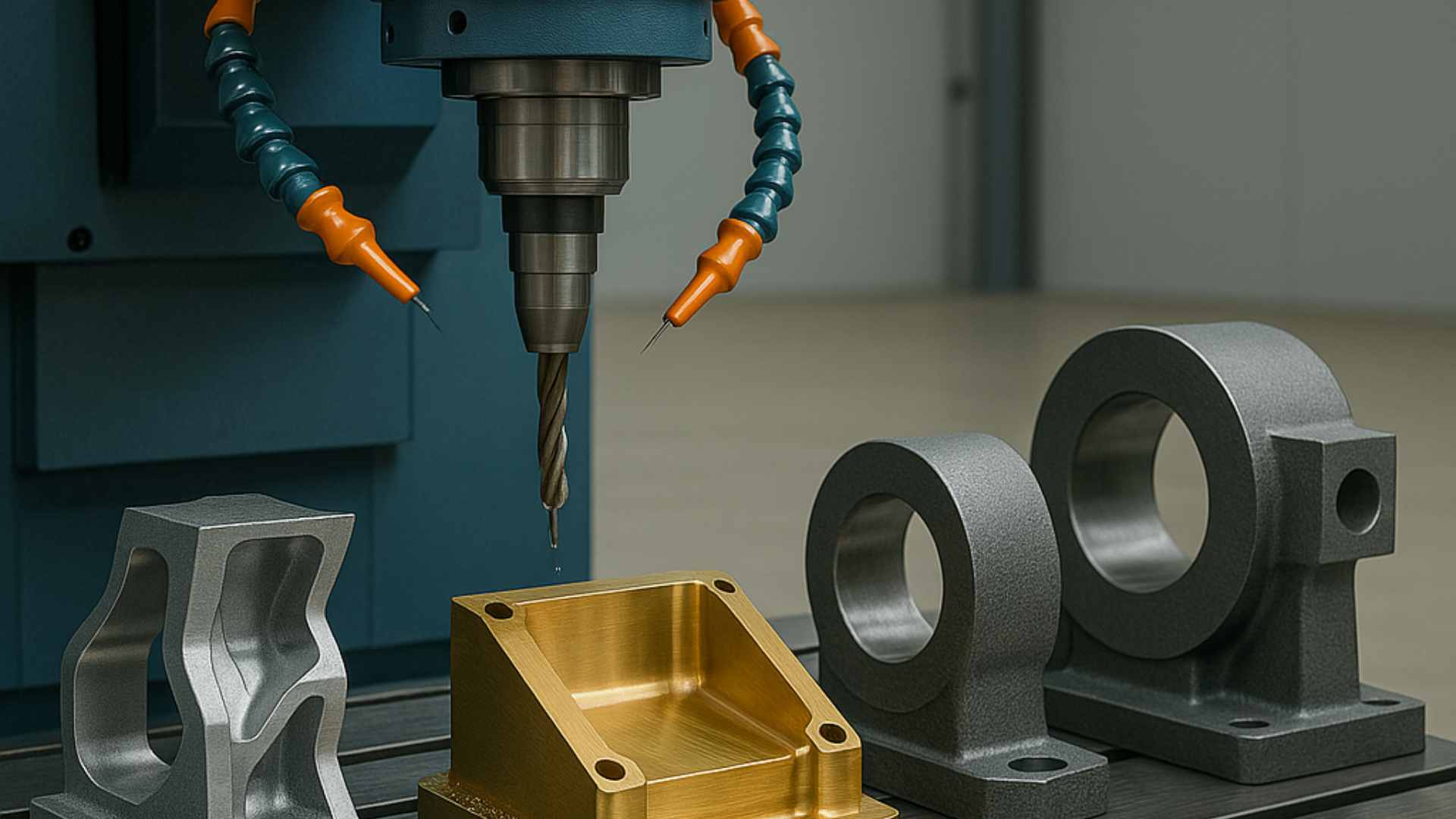
July 09, 2025
Share:
Introduction
The manufacturing landscape is evolving rapidly, and CNC (Computer Numerical Control) machining is at the forefront of this transformation. One of the most significant advancements in recent years is multi-material machining, where CNC machines process different materials simultaneously or in a single production cycle. This approach is becoming increasingly common in industries such as aerospace, automotive, medical, and electronics, where products often require components made from different materials.
While multi-material machining offers several advantages, including improved efficiency and reduced production time, it also presents unique challenges. The varying properties of different materials demand precise tool selection, speed adjustments, and machining strategies. At the same time, innovative technologies are making it easier for manufacturers to achieve accuracy and consistency when working with multiple materials.
This blog delves into the challenges, innovations, and future of multi-material machining, providing insights into how CNC technology is adapting to this growing trend.
Understanding Multi-Material Machining
Multi-material machining involves the processing of two or more distinct materials within the same machining cycle. This can be achieved in different ways:
- Single-Part Machining: When a single part is composed of different materials, requiring multiple machining operations.
- Composite Machining: Processing composite materials with multiple layers or embedded components.
- Hybrid Machining: Combining different manufacturing techniques, such as CNC milling with laser cutting or 3D printing, to handle mixed materials.
Industries increasingly rely on multi-material components for their strength, functionality, and reduced weight. For example, aerospace components often consist of titanium, aluminum, and carbon fiber composites, while automotive parts may combine steel with plastic or rubber elements.
Challenges in Multi-Material Machining
Despite its advantages, multi-material machining presents several challenges due to the varying properties and behaviors of different materials. These challenges include:
1. Tool Wear and Selection
One of the primary issues in multi-material machining is the varying hardness and abrasiveness of different materials. For instance, machining aluminum and titanium together requires different cutting speeds and tools. When both are processed in the same cycle, the tools experience uneven wear. This can lead to inaccuracies, reduced tool life, and inconsistent surface finishes.
Solution:
Manufacturers are increasingly using advanced tool coatings and materials such as carbide and polycrystalline diamond (PCD) to improve durability and extend tool life when machining multiple materials.
2. Varying Cutting Parameters
Each material has its own optimal cutting speed, feed rate, and depth of cut. Machining different materials in a single operation makes it difficult to maintain optimal parameters for all materials simultaneously. For example, cutting plastics and metals together requires different spindle speeds and feed rates, making it challenging to achieve uniform results.
Solution:
Modern CNC machines utilize adaptive machining software that automatically adjusts cutting parameters based on the material being processed. This ensures consistent quality and precision without operator intervention.
3. Thermal Expansion and Heat Management
Different materials expand and contract at different rates when exposed to heat. During multi-material machining, this can lead to dimensional inaccuracies and distortions. Heat management becomes crucial, especially when working with composites or thermoplastics, which are sensitive to temperature changes.
Solution:
Manufacturers are adopting coolant systems and thermal compensation technologies to regulate temperatures during machining. This prevents heat-related distortions and ensures dimensional stability.
4. Material Compatibility Issues
When machining dissimilar materials, their chemical and mechanical compatibility must be considered. For instance, certain materials may react negatively to coolants or cutting fluids, causing contamination or corrosion. Additionally, differences in hardness and density can lead to uneven material removal rates.
Solution:
CNC operators are increasingly using specialized cutting fluids and multi-material clamps that prevent cross-contamination and enhance stability during machining.
5. Complex Programming Requirements
Multi-material machining often requires intricate CNC programming. Operators must define separate toolpaths, cutting parameters, and tool changes for each material. This makes programming more complex and time-consuming.
Solution:
Modern CNC machines are equipped with advanced CAD/CAM software that simplifies multi-material programming. Automated toolpath generation and simulation features help reduce programming errors and streamline the process.
Innovations Driving Multi-Material Machining
To overcome the challenges of multi-material machining, the CNC industry is adopting several innovative solutions. These technological advancements are enhancing precision, efficiency, and reliability.
1. Hybrid CNC Machines
One of the most significant innovations is the emergence of hybrid CNC machines. These machines combine traditional CNC milling, turning, or drilling with additive manufacturing (3D printing) or laser cutting capabilities. This allows manufacturers to create complex, multi-material components in a single setup, reducing production time and costs.
2. Multi-Tool Spindles
CNC machines are now equipped with multi-tool spindles capable of switching between tools rapidly. This enables seamless transitions between materials, enhancing efficiency and precision. For example, in the automotive industry, machines can switch from a steel-cutting tool to a plastic-drilling tool without interrupting the machining cycle.
3. Intelligent Toolpath Optimization
Advanced CNC software solutions use AI-powered algorithms to optimize toolpaths for multi-material machining. These algorithms analyze the properties of each material and automatically adjust feed rates, speeds, and cutting strategies. This minimizes tool wear and ensures consistent quality across different materials.
4. Adaptive Machining and Real-Time Monitoring
Real-time monitoring systems are becoming increasingly common in CNC workshops. These systems track tool wear, material behavior, and cutting conditions. By using adaptive machining, CNC machines can adjust parameters on the fly, preventing defects and maintaining precision, even with mixed materials.
Applications of Multi-Material Machining
Multi-material machining is widely used across various industries, including:
- Aerospace: Components made from titanium, aluminum, and composites require precision multi-material machining to ensure strength and lightweight properties.
- Automotive: Hybrid parts combining metals and plastics for fuel efficiency and performance benefit from multi-material CNC processes.
- Medical Devices: Implants and surgical tools often require the combination of biocompatible metals and plastic parts, necessitating precise multi-material machining.
- Electronics: PCBs and electronic enclosures often involve multiple materials, such as copper and polymer, processed together for compact and efficient designs.
Conclusion
Multi-material machining is revolutionizing CNC manufacturing by enabling the efficient production of complex components. Despite the challenges of tool wear, thermal expansion, and programming complexity, innovations such as hybrid machines, intelligent toolpaths, and adaptive machining are making multi-material machining more feasible and efficient. As the demand for multi-material components continues to grow, CNC technology will play a pivotal role in driving precision, efficiency, and innovation in modern manufacturing.
Explore Related Machines from Sahil Machines:
FAQ
Multi-material machining refers to the process of cutting, milling, or shaping two or more different materials in the same CNC machining cycle.
It is challenging due to differences in hardness, cutting parameters, and thermal properties between materials, which can lead to uneven tool wear and dimensional inaccuracies.
Industries such as aerospace, automotive, medical, and electronics frequently use multi-material machining to produce complex and durable components.
Modern CNC machines use adaptive software, multi-tool spindles, and real-time monitoring systems to adjust cutting parameters based on material properties.
Carbide, ceramic, and polycrystalline diamond (PCD) tools are commonly used to withstand the varying hardness and abrasiveness of different materials.
Follow Us:
Latest Posts
Get in touch with us about anything.
Connect with our team to explore the alloy solutions and machinery expertise you need.