CNC Machining for Prosthetics: Enhancing Medical Innovations with Precision Manufacturing
Discover how CNC machining plays a vital role in the creation of advanced prosthetics by enabling precision manufacturing, patient-specific customization, and rapid innovation in the medical field.
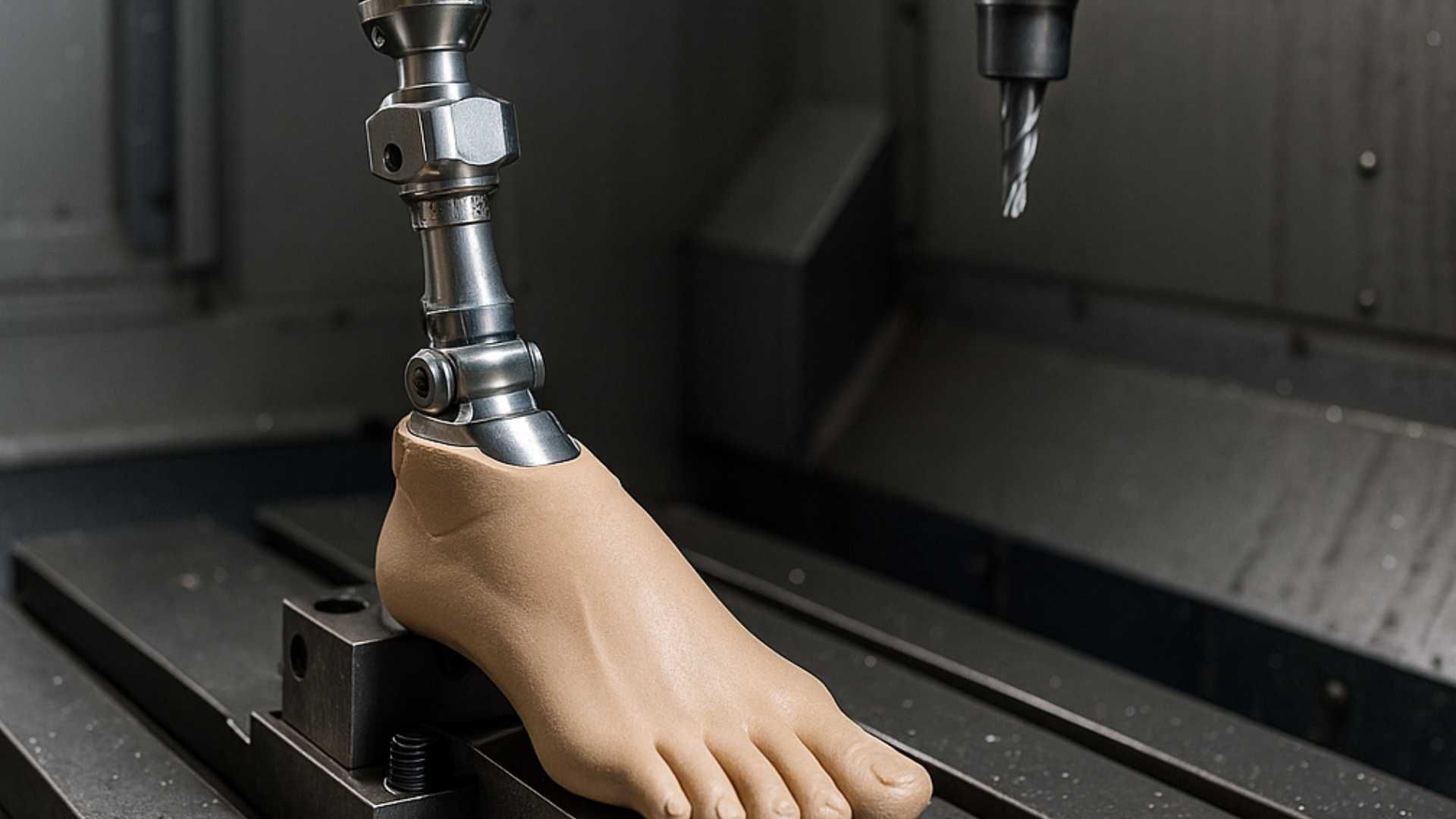
July 09, 2025
Share:
In today’s rapidly advancing medical field, CNC machining has emerged as a vital tool in transforming the way prosthetics are designed, developed, and delivered. The demand for personalized, high-quality prosthetics has skyrocketed as medical science intersects with advanced engineering. One of the key enablers of this transformation is Computer Numerical Control (CNC) machining, a technology known for its precision, reliability, and efficiency.
CNC machining is not just enhancing the production of prosthetics—it’s redefining the future of rehabilitative care.
The Rise of Precision in Medical Manufacturing
Prosthetic devices must be accurate, durable, biocompatible, and comfortable for long-term use. Traditionally, crafting prosthetics involved labor-intensive manual processes, which could lead to inconsistent results and longer production cycles.
CNC machining changes that by offering:
- High-precision output within microns
- Repeatability for scalable production
- Customization for individual patients
- Material flexibility, including titanium, stainless steel, and medical-grade plastics
This level of precision ensures that every component—whether a joint, socket, or limb—fits perfectly, functions optimally, and integrates seamlessly with the patient’s body and lifestyle.
Why CNC Machining is Perfect for Prosthetics
1. Patient-Specific Customization
Every human body is unique, and prosthetics must reflect that. CNC machines, when combined with 3D scanning and CAD (Computer-Aided Design), allow for the creation of personalized prosthetic devices tailored to the exact contours and biomechanics of the user.
This results in:
- Better fit and comfort
- Enhanced mobility and functionality
- Fewer adjustments or remakes
2. Rapid Prototyping and Development
CNC machining allows designers and medical engineers to prototype new prosthetic components quickly, test them, and refine the design in shorter cycles. This accelerates innovation, reduces time to market, and enables faster delivery for patients in need.
3. Advanced Material Capabilities
CNC machines can work with a wide range of biocompatible materials essential for medical use, including:
- Titanium for strength and lightness
- Aluminum alloys for lightweight mobility components
- PEEK (polyetheretherketone) and UHMWPE (ultra-high-molecular-weight polyethylene) for joints and sockets
- Carbon fiber for high-performance prosthetics
These materials provide durability, lightweight properties, and flexibility—crucial for both functionality and comfort.
4. Improved Quality Control
Precision machining ensures tight tolerances and consistent results, making the manufacturing process more reliable. CNC systems can be integrated with quality control software and inspection tools, reducing the risk of defects and improving compliance with medical regulations and certifications.
Applications of CNC Machining in Prosthetics
- Limb Prosthetics: CNC machining is used to manufacture sockets, joints, and connectors for artificial legs, arms, and hands, offering seamless movement and enhanced control.
- Cranial and Maxillofacial Implants: Highly intricate and patient-specific plates or implants can be milled with CNC technology for trauma, surgery, or reconstructive procedures.
- Spinal and Orthopedic Devices: CNC machining produces precise orthopedic aids, such as spinal rods or hip components, often integrated with prosthetic systems.
- Bionic Prosthetics: CNC helps in the development of parts for sensor-integrated or robotic prosthetics, where internal components require exact tolerances.
Impact on Medical Innovation and Patient Outcomes
CNC machining doesn’t just make prosthetics—it makes better prosthetics. The impact is profound:
- Faster recovery due to better fit and function
- Enhanced patient mobility and quality of life
- Wider accessibility as automation reduces costs
- Ongoing innovation as engineers push the boundaries of design
With rising demand for prosthetics globally due to accidents, congenital disabilities, and war injuries, CNC technology enables scalable, reliable, and humane solutions.
Challenges and Future Potential
While CNC machining offers many benefits, it does come with challenges in the medical field:
- High initial setup cost for specialized machines and tooling
- Skilled labor requirement for programming and design
- Regulatory hurdles around certification and compliance
That said, the future of CNC machining in prosthetics is bright. Advancements in AI-powered machining, digital twin simulation, and integration with 3D printing are set to redefine prosthetic design and fabrication even further.
Imagine a future where a patient’s limb can be scanned, modeled, machined, and delivered within 24 hours—all made possible by automation, data, and precision manufacturing.
Conclusion
CNC machining for prosthetics represents the perfect synergy between engineering precision and medical compassion. It bridges the gap between mass production and personalized care—producing devices that don’t just meet medical standards but transform lives. As innovation in materials, AI, and digital modeling continues to grow, CNC machining will remain a cornerstone in the future of advanced, accessible, and life-changing prosthetic solutions.
Explore more from Sahil Machines
Want to know how Sahil Machines is shaping the future of medical and precision manufacturing?
FAQ
CNC machining allows for high precision, repeatability, and customization—essential qualities for manufacturing prosthetics that are both functional and comfortable.
Yes, using CAD/CAM software and 3D scanning, CNC machines can produce parts tailored to a patient’s unique anatomy, ensuring a better fit and enhanced usability.
Common materials include titanium, aluminum, carbon fiber composites, and medical-grade plastics like PEEK or UHMWPE, all chosen for their strength, weight, and biocompatibility.
By automating cutting, milling, and shaping processes, CNC machining drastically reduces manual labor and speeds up the prototyping and production phases.
While the upfront investment is high, CNC machining offers long-term savings through reduced waste, fewer remakes, better quality, and scalable production—making it highly cost-effective in the long run.
Follow Us:
Latest Posts
Get in touch with us about anything.
Connect with our team to explore the alloy solutions and machinery expertise you need.