A Guide to Retro-Fitting Old CNC Machines with Modern Control Systems
Learn how retrofitting old CNC machines with modern control systems can enhance performance, reduce downtime, and improve efficiency. This guide covers the benefits and steps involved in upgrading older machines.
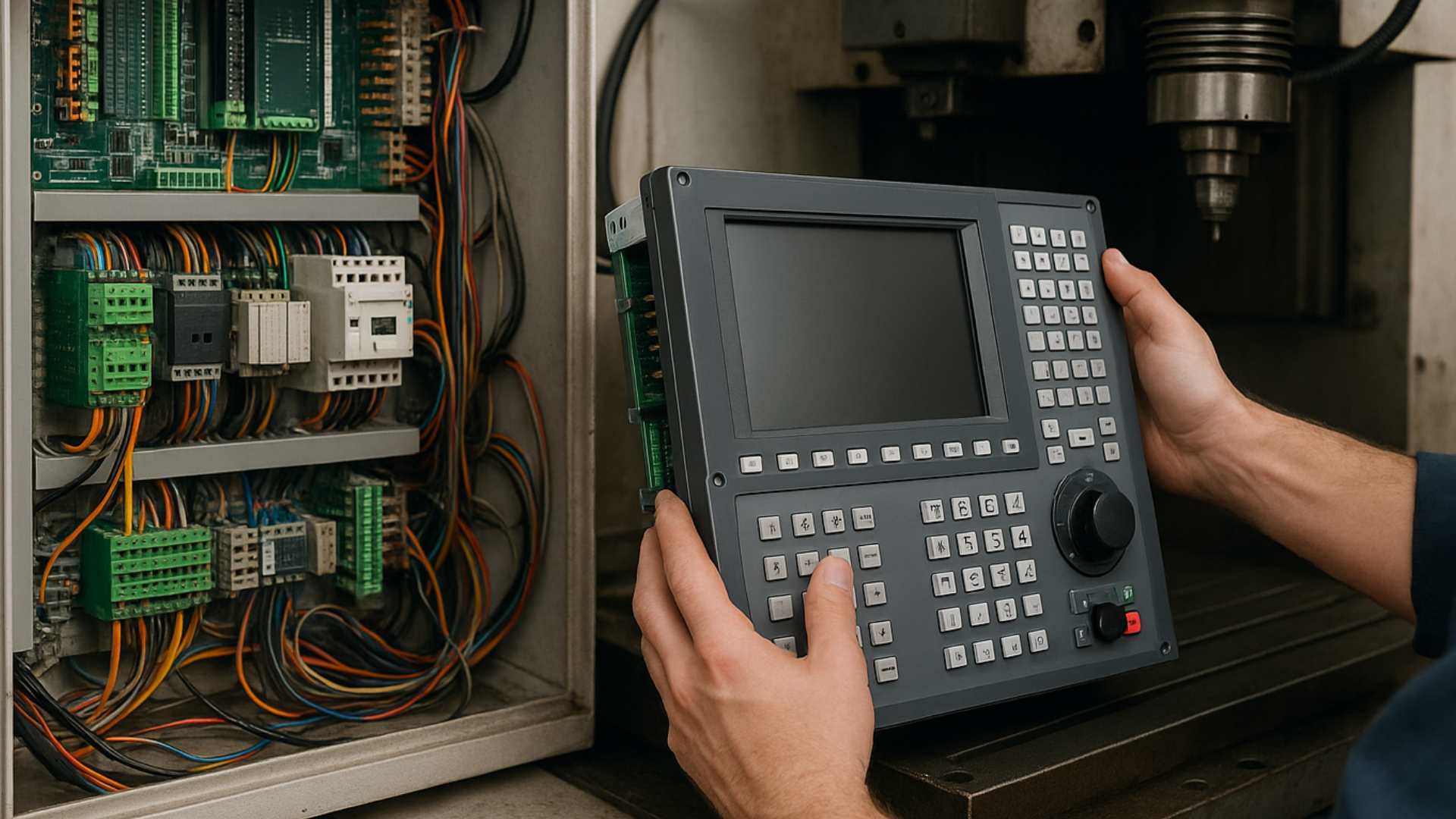
July 09, 2025
Share:
In the fast-evolving world of manufacturing, keeping up with technological advancements is key to maintaining a competitive edge. For many businesses, this often means upgrading old equipment to take advantage of modern technologies. One such upgrade that can significantly improve performance and efficiency is retrofitting old CNC (Computer Numerical Control) machines with modern control systems.
Although purchasing brand-new CNC machines may seem like the obvious choice, retrofitting offers a more cost-effective alternative that can bring older machines back to life with improved functionality. In this guide, we will explore the process of retrofitting old CNC machines, the benefits it brings, and how it can enhance your operations.
What is CNC Retrofitting?
CNC retrofitting refers to the process of upgrading an older CNC machine with new control systems, including hardware and software, to improve its performance. This typically involves replacing outdated CNC controls, motors, drives, and other components with newer technologies while retaining the original mechanical components of the machine, such as the bed, spindle, and structure. Retrofitting allows manufacturers to extend the life of their existing machines, avoiding the high costs associated with purchasing new equipment, while still benefiting from enhanced capabilities like higher precision, faster speeds, and improved automation.
Why Retrofit an Old CNC Machine?
There are several compelling reasons why retrofitting an old CNC machine is an attractive option for businesses:
1. Cost Savings
One of the biggest advantages of retrofitting is the cost savings compared to purchasing a brand-new CNC machine. The cost of retrofitting an old CNC machine is typically a fraction of the price of buying new equipment, and the upgrade can give your machine a fresh lease of life. This is especially beneficial for smaller manufacturers or businesses that have older, high-quality machines that still have years of life left but need a modern control system to stay competitive.
2. Improved Performance and Efficiency
Modern control systems offer advanced features that can significantly enhance the performance of your CNC machine. These features include increased precision, faster processing speeds, better tool management, and the ability to integrate with other systems in a smart factory. By retrofitting, you’re effectively transforming your old machine into a high-performance workhorse capable of handling the demands of modern manufacturing.
3. Better Software and User Interface
Older CNC machines often come with clunky, outdated user interfaces that can make operation difficult and time-consuming. Modern control systems provide intuitive software with easy-to-use graphical interfaces, making the machine easier to program and operate. These advanced systems also allow for remote monitoring and diagnostics, reducing downtime and troubleshooting time.
4. Extended Machine Lifespan
Retrofitting a CNC machine with a modern control system can extend its lifespan by improving its reliability and precision. Newer systems offer enhanced durability, reduced wear, and better energy efficiency, all of which contribute to a longer, more productive life for your existing equipment.
5. Compatibility with Industry 4.0
With the rise of Industry 4.0, smart factories, and the Internet of Things (IoT), retrofitting your CNC machine allows you to bring your equipment into the connected world. Modern control systems are designed to integrate seamlessly with other smart machines, allowing for data collection, real-time monitoring, and predictive maintenance.
How to Retrofit an Old CNC Machine: A Step-by-Step Process
While the process of retrofitting can be complex, it generally follows a few standard steps. Here’s a basic overview of the steps involved:
1. Assess the Existing Machine
Before beginning the retrofit process, it’s essential to assess the condition of the existing CNC machine. This involves evaluating its mechanical components, such as the bed, spindle, and axis drives. If the machine is still in good condition structurally, retrofitting will be a viable option. However, if there are significant issues with the machine’s physical components, it may be more cost-effective to consider purchasing a new machine.
2. Choose the Right Control System
Once you’ve determined that the machine is a suitable candidate for retrofitting, the next step is to choose the right modern control system. There are various manufacturers offering CNC control systems, such as Siemens, Fanuc, and Allen-Bradley, each with its own set of features. The control system you choose should be compatible with your machine’s mechanical components and meet the requirements of your operations in terms of precision, speed, and flexibility.
3. Upgrade the Drive Motors and Feedback Devices
Modern CNC systems require advanced drive motors and feedback devices for accurate positioning and performance. During the retrofit, you’ll need to replace the old motors and add encoders or resolvers to provide real-time feedback to the control system. This ensures that your machine can perform high-precision operations with minimal errors.
4. Wiring and Electrical Upgrades
Retrofitting typically involves rewiring the machine to accommodate the new control system and components. This can include upgrading the power supply, installing new electrical connections, and ensuring proper grounding to ensure the machine runs smoothly and safely.
5. Install and Configure the New Control System
Once the hardware has been upgraded, the next step is to install and configure the new control system. This step involves setting up the machine's parameters, calibrating the axes, and programming the machine to communicate with the new system. The new control system may require custom software programming to ensure compatibility with your existing CNC programs and tools.
6. Testing and Commissioning
After the retrofit is complete, it’s important to thoroughly test the machine to ensure everything is functioning properly. This includes running test programs, verifying machine movements, and performing trial cuts. Any issues that arise during testing should be addressed before the machine is put into full production.
Benefits of Retrofitting: A Final Thought
While retrofitting is an investment of time and resources, it offers numerous advantages that can significantly improve your operations. From cost savings to improved performance and longevity, upgrading your CNC machine with a modern control system can enhance the efficiency, precision, and competitiveness of your manufacturing processes. In addition, retrofitting helps reduce your carbon footprint by extending the life of your existing machines and reducing the need for new equipment.
Explore More from Sahil Machines
For more insights into CNC machines and modern upgrades, check out the following resources from Sahil CNC:
FAQ
CNC retrofitting is the process of upgrading an old CNC machine by replacing its outdated control system and other components with modern, more efficient technology.
Retrofitting is a more cost-effective option compared to buying a new CNC machine. It allows you to extend the life of your existing equipment while benefiting from the latest technology.
The time required for retrofitting depends on the complexity of the machine and the scope of the upgrade. Typically, the process can take anywhere from a few days to several weeks.
In most cases, yes. However, older machines with severe mechanical damage or structural issues may not be suitable candidates for retrofitting.
The main benefits include cost savings, improved performance and efficiency, better software interfaces, extended machine lifespan, and the ability to integrate with Industry 4.0 technologies.
Follow Us:
Latest Posts
Get in touch with us about anything.
Connect with our team to explore the alloy solutions and machinery expertise you need.