A Deep Dive into High-Precision Micro-Machining with CNC Technology
High-precision micro-machining with CNC technology enables the production of ultra-small, complex components with extreme accuracy. This blog explores the process, its applications, challenges, and innovations.
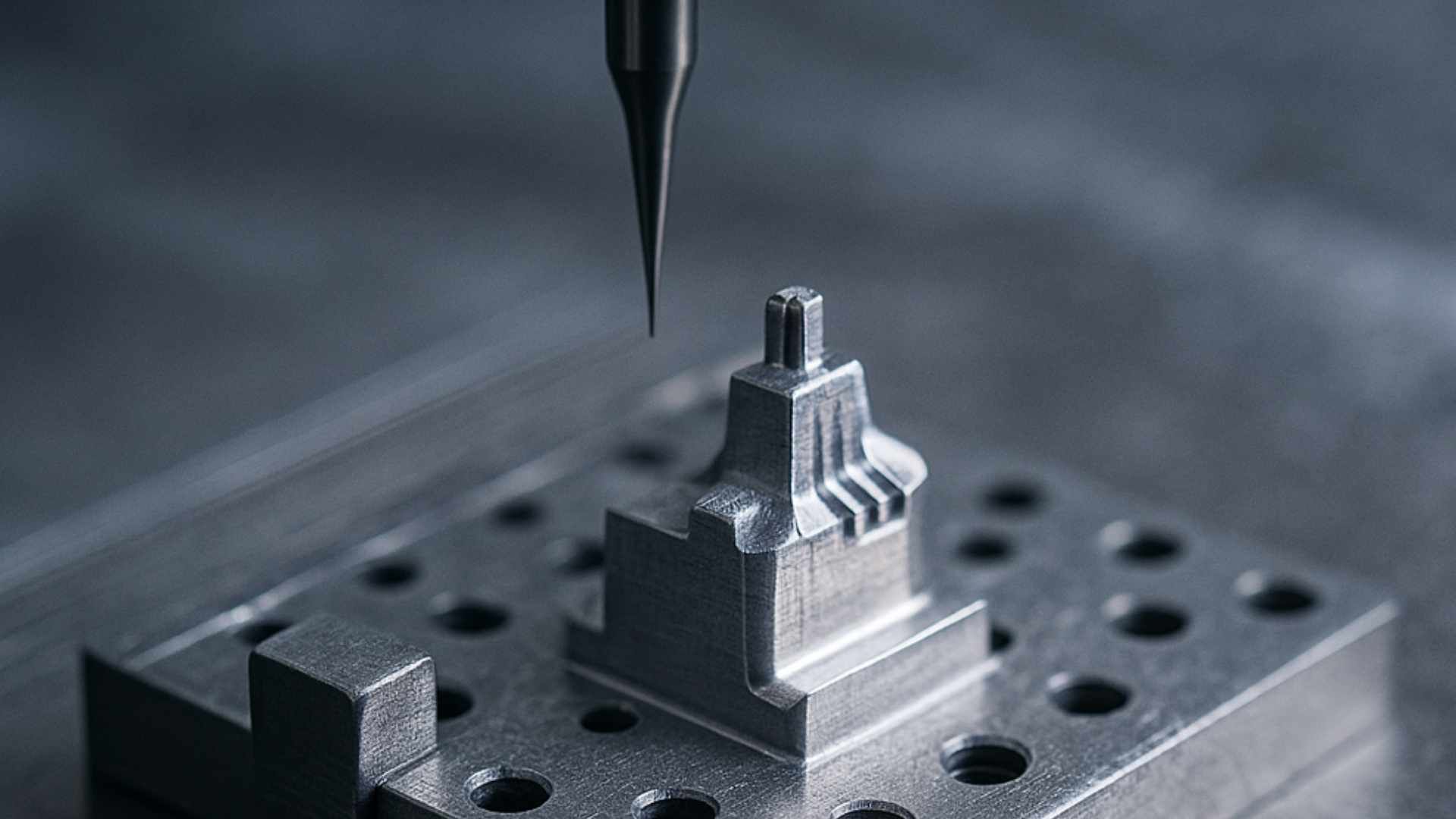
July 09, 2025
Share:
In an age where devices are shrinking and precision is paramount, high-precision micro-machining has emerged as one of the most revolutionary technologies in modern manufacturing. Powered by advanced CNC (Computer Numerical Control) systems, this technique enables the creation of intricate parts that are often too small to be seen clearly with the naked eye — yet critical to the performance of everything from pacemakers to satellites.
Micro-machining is not just about working small; it’s about working extremely precisely at a small scale. This discipline requires a fine blend of cutting-edge tools, smart software, and deep process understanding. The beauty of CNC-based micro-machining lies in its ability to consistently produce miniature parts with tolerances often tighter than a human hair’s width. But how exactly does it work, and where is it making the biggest impact? Let’s find out.
Understanding Micro-Machining in the CNC World
Micro-machining involves creating tiny components with high dimensional accuracy and exceptional surface finishes. These parts may range from a few millimeters down to fractions of a millimeter in size. The tolerances can be as tight as ±1 micron (0.001 mm), requiring machines that are far more stable, responsive, and precise than standard CNC systems.
Traditional CNC machines, while accurate, aren't always capable of working efficiently at the micro scale. That’s where specialized high-precision CNC equipment comes in, with features like high-speed spindles, micro-tool holders, and advanced feedback systems.
What sets micro-machining apart is the extreme focus on accuracy, repeatability, and surface integrity. A slight deviation or tool vibration can ruin an entire component, making every aspect of the process — from material choice to tool path design — critically important.
Where Micro-Machining Makes an Impact
The applications of micro-machining are vast and continue to grow as industries demand more compact, high-performance components. Among the most important sectors benefiting from this technology are:
Medical and Healthcare:
In the medical field, micro-machining is used to produce components like stents, implants, micro-surgical tools, and diagnostic equipment. The parts must meet stringent standards for safety and biocompatibility, and CNC micro-machining allows manufacturers to deliver those requirements with confidence.
Electronics and Semiconductors:
As devices become smaller and smarter, the need for tiny connectors, housings, circuit pathways, and sensor elements grows rapidly. Micro-machining ensures that even the most complex geometries can be reproduced at a minuscule scale with high fidelity.
Aerospace and Defense:
Here, lightweight and compact components can make a significant difference in fuel efficiency and overall performance. Micro-machined parts are often used in advanced propulsion systems, guidance units, and micro-electromechanical systems (MEMS).
Optics and Watchmaking:
From intricate lens holders to precision gears in luxury watches, these industries demand not only technical performance but also aesthetic perfection. CNC micro-machining allows for the creation of fine, elegant components that function flawlessly and look beautiful.
What Makes High-Precision Micro-Machining Possible
The success of micro-machining relies on a combination of machine features, control systems, tooling, and environmental conditions. Unlike traditional machining, even thermal expansion or microscopic vibrations can affect quality, making stability and control critical.
Some key enablers include:
-
High-Speed Spindles: These are essential for handling extremely small cutting tools. Speeds often exceed 60,000 RPM to avoid tool deflection and breakage.
-
Micro-Tools: Tools used in micro-machining may be smaller than 0.1 mm in diameter and require special coatings and geometry to maintain edge sharpness and minimize wear.
-
Precision Feedback Systems: CNC systems equipped with linear scales and encoders provide real-time positional accuracy to the nanometer level.
-
Advanced Tool Path Strategies: Optimized tool paths and cutting strategies reduce the load on tools and help in achieving smooth, burr-free finishes.
-
Cleanroom and Vibration-Free Environments: Since even the slightest contamination or vibration can disrupt machining, many setups use cleanroom conditions or isolate machines on anti-vibration platforms.
Challenges That Come with Going Micro
As impressive as it is, micro-machining comes with its own set of hurdles. Handling, inspecting, and assembling parts at this scale demands specialized knowledge and equipment.
Tool Breakage and Wear:
Due to their small size and fragility, micro-tools are prone to faster wear and sudden breakage. This demands constant monitoring and often limits tool life.
Material Behavior:
Materials don’t behave the same at the micro level. Their microstructure, grain boundaries, and internal stresses become far more significant. This calls for tailored approaches to machining parameters.
Quality Inspection:
Conventional measuring tools are useless here. High-end microscopes, scanning electron microscopes (SEM), or laser interferometry are used for checking tolerances and surface quality, often adding to the cost and time.
Where Micro-Machining is Headed
With growing demand in fields like robotics, AI hardware, biomedical nanotech, and IoT, micro-machining is evolving fast. Machine learning and AI are increasingly being used to predict tool wear and optimize cutting conditions in real-time. Hybrid systems that combine additive manufacturing (like micro 3D printing) with subtractive CNC machining are also gaining traction.
Moreover, automation in micro-part handling and inspection is advancing rapidly, reducing human error and increasing output quality. In the future, we’re likely to see fully autonomous micro-factories capable of running 24/7 at sub-micron precision — a significant leap for sectors like space, nanotech, and quantum computing.
Conclusion
High-precision micro-machining represents a blend of science, engineering, and art — all working at a scale that’s barely visible to the eye, but vital to the future. With CNC technology at its core, it unlocks possibilities across industries that require compact, complex, and reliable components. As tools and technology continue to evolve, the ability to machine at the micro-level will only become more powerful and accessible — and that’s a future worth watching closely.
Explore More from Sahil Machines
Explore cutting-edge CNC solutions and services to take your manufacturing to the next level:
FAQ
Most CNC micro-machining setups can maintain tolerances within ±1 micron, depending on the machine and material.
Yes. Common materials include stainless steel, titanium, aluminum, and engineering plastics like PEEK or PTFE.
Tool diameters can go as small as 10 microns (0.01 mm), though handling and setup become extremely delicate at that level.
With the right automation and process control, it is. Many industries now rely on it for high-volume production of micro components.
Through a mix of ultra-high spindle speeds, precise tool paths, and post-machining polishing or finishing where needed.
Follow Us:
Latest Posts
Get in touch with us about anything.
Connect with our team to explore the alloy solutions and machinery expertise you need.